At ATB Technologies, we provide IT support for manufacturing companies that helps them to reduce downtime, plan effectively for the future, and ensure that production processes run smoothly.
Manufacturing firms most often come to us with two technology issues: ERP inefficiencies and IT challenges. Our in-house software developers customize clients’ current ERP solutions to streamline workflows and reporting. Our expert support staff proactively manage IT systems, turning our clients’ IT into an advantage.
If you’re considering IT support for your manufacturing company, get in touch with us today for a free consultation.
If you’re looking to learn more about how to approach IT support for manufacturing – keep reading. We’re going to cover a variety of critical considerations that manufacturers must make in regard to their IT systems. We’ll look at questions like:
- What IT solutions do manufacturers need?
- How should manufacturers create an IT plan?
- What are the top manufacturing IT trends?
- What should a manufacturing IT policy include?
- What are the top IT challenges for manufacturers?
- How should manufacturers approach cybersecurity?
- What ERP solution is best for manufacturers?
- How can manufacturers use data analysis?
Our hope is that, through a better understanding of these topics, you’ll be able to construct an IT approach that positions your company to maximize your technology. Your IT is an essential function – and if you get it right, it can be an advantage.
Ready? Let’s dive in.
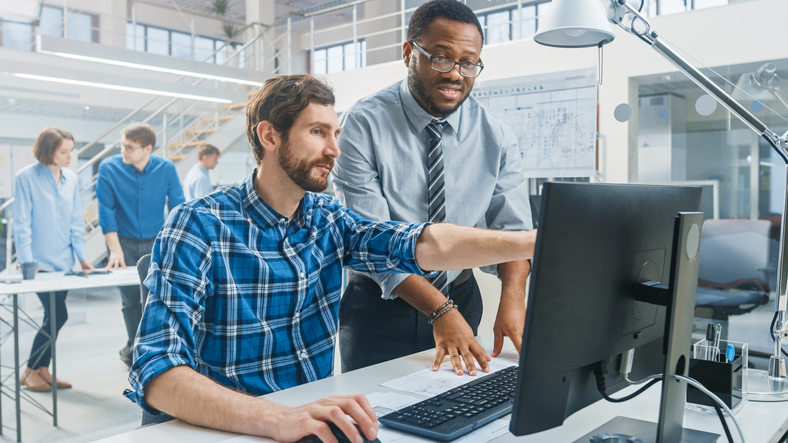
What IT solutions do manufacturers need?
First, let’s establish a foundational understanding of what manufacturing information technology looks like. Sure, manufacturing companies need IT support – but what, exactly, should be supported?
While IT solutions will vary across different manufacturing facilities and business contexts, here are a few of the standard solutions that manufacturers nearly always need.
A robust network.
In today’s internet-driven age – where so many systems are online and where automation is assumed – it’s crucial that manufacturing firms have robust networks. By robust, we mean that networks should both be able to easily support the load of facility functions and be hardened against cybersecurity threats.
It’s worth noting that, in addition to the importance of traditional networks, manufacturers would do well to consider the design, implementation, and maintenance of any IoT networks. Thanks to the variety of machines on these networks, they can sometimes lag behind in security and efficiency – but they’ll only become more important as connectivity becomes more ubiquitous.
Server and workstation support.
Manufacturing IT solutions should also support servers and workstations. Most often, these are stored or arranged in the facility office space off of the production floor. Accordingly, their support tends to be tied into the support of the facility itself.
Increasingly, though, cloud-based servers may be used to run facility applications. And remote work is increasingly common, so office-based employees may choose to work from different locations.
The key is that systems are kept online and running smoothly – and that help is easily accessible whether employees are working at the facility or at other locations. Helpdesk support can be a viable solution for this.
An ERP system.
Now, we’re getting a bit more specialized. Not every industry needs an optimized enterprise resource planning solution – but manufacturers (at least those operating at any sort of scale) do.
ERPs are software platforms that provide both visibility of and control over data across business processes. They integrate functions like finance, HR, supply chain, operations, and reporting into a single system, where traditionally these functions would’ve had their own processes and little ability to share data between them.
It’s important that manufacturers get their ERP solutions right. Margin matters, and inefficient data management can add up to big costs over time. At ATB, we help companies with custom ERP development and consulting to ensure that systems are creating advantages.
If you aren’t sure your ERP is working for you, give us a call.
Support for specialized systems.
Finally, technology for manufacturing companies should include support for specialized systems.
Admittedly, this is a bit of a catch-all; covering every technology option in this space isn’t realistic, but it’s important to note that most manufacturing companies have some sort of specialized system tailored to their industry and needs. IT support must take this reality into account.
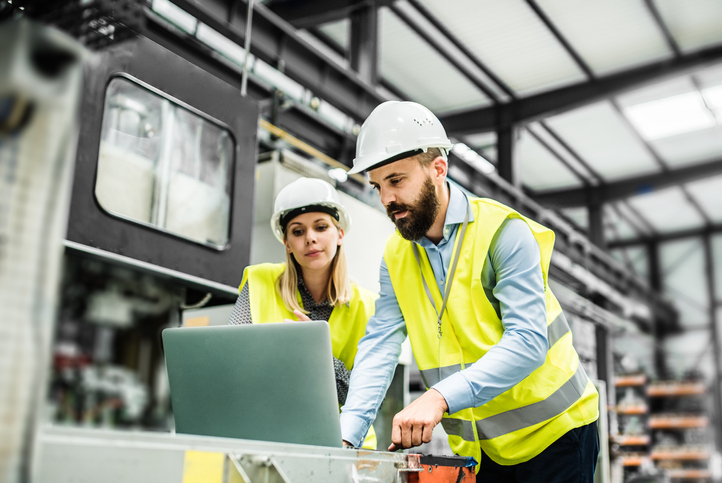
How should manufacturers create an IT plan?
We’ve established a foundation of manufacturing IT solutions – now, it’s time to account for how those solutions might change.
Manufacturers must plan for their IT to evolve as their company develops and the technology environment around them changes. While the specifics of a plan will vary greatly depending on context, here are the core steps to follow.
Evaluate the current state of your IT.
Any plan should begin at the beginning: with an analysis of where you stand. Too many companies start by planning for the future. The problem with this approach is that it fails to account for factors in the present.
For instance, it might be wonderful to upgrade your network devices – but doing so might require redoing the cabling in your facility in order to support newer protocols. In this scenario, you couldn’t plan for one upgrade without planning for the other.
If you don’t account for the realities of where you’re starting from, your IT plan won’t make sense.
Here are a few questions to ask:
- What technologies are we currently using?
- What technology is working well?
- What technology needs to be improved?
- What needs to be updated this year?
- What will need to be updated within three years?
Predict the future state of your facility.
Once you’ve evaluated the current state of your manufacturing IT setup, you can move to predicting the future state of your facility. This will help you to identify the gaps between your current state and your future needs.
Set a target date for your plan (1/3/5 years) and ask questions like:
- How will my processes change?
- How many users will I have?
- What will the space look like?
- What will be outdated?
Create a roadmap to navigate growth.
With your current state and future state described, you can begin to chart a roadmap toward improving your IT solutions. The form that this takes is up to you, but remember – plans can be useless, but planning is essential.
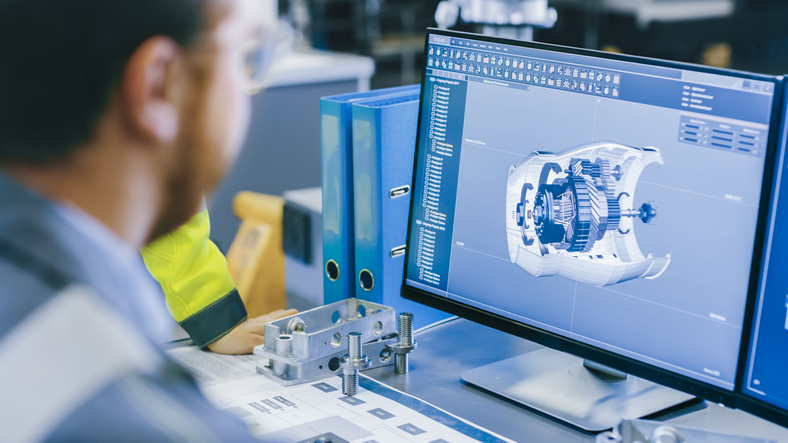
What are the top manufacturing IT trends?
As you consider your IT plan, you’ll do well to pay attention to the trends in manufacturing IT. In the past two or three decades, manufacturing has changed substantially, and the progress shows no signs of abating as we move through the 2020s.
Here’s what to watch.
IoT
The Internet of Things became a buzzword a few years ago for good reason: experts estimate that there will be 25 billion connected things in use by 2021. That’s up nearly 80% from counts in 2019. IoT technologies are already in widespread use in manufacturing, often with fascinating applications.
Supply chain management, for example, looks vastly different today than it did a decade ago, as connected devices track chains in real-time and either automate backfill or pass data to decision makers. The next decade promises more innovation.
Big data is a big deal.
Big data is another buzzword that’s worthy of its hype. The concept is pretty simple at a basic level; “big data” just refers to huge amounts of data. The power of big data is that processing it effectively can allow for big insights.
Manufacturing is inherently data-driven, and the facilities that are able to best harness their data to improve processes and decision-making will have significant advantages.
The growth of ERP solutions.
This is related to the topic of data: ERP solutions are increasingly enabling manufacturing firms to effectively manage their data (and the processes it represents). ERPs have been around for a few decades, so they aren’t a trend in the sense that they’re new as a concept – but they are becoming more and more instrumental in manufacturing processes. The next decade will see successful manufacturers thrive with largescale data integrations to make workflow more efficient.
Predictive maintenance.
Finally, this is another trend that isn’t new in concept but is being newly applied. Manufacturers have traditionally understood the value of preventative maintenance on their machines – it’s obviously better to change the oil regularly than to let the machine break.
Now, the concept of preventative maintenance (fixing problems before they arise) is being combined with IoT data to identify equipment deficiencies before they cause problems – an approach called predictive maintenance. At a basic level, for example, this might mean having an IoT-connected machine send an alert when fluid levels are low. At a higher level, it might mean a machine recognizing a variety of stress factors and sending an alert predicting an outage within three days. Regardless, the outcome of this is less downtime.
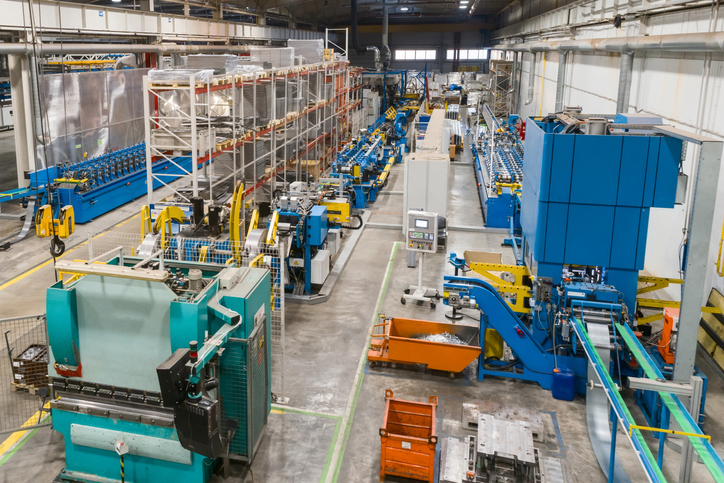
What should a manufacturing IT policy include?
We’ve covered how manufacturing IT is changing. Now, let’s take a look at how you can bring stability into your environment through an IT policy.
IT policies are documented protocols that define the rules and procedures for users of IT assets. Basically, an IT policy should inform your people in the best ways to use your technologies. Here’s what should likely be included.
Acceptable use guidelines.
An acceptable use policy delineates the ways in which IT resources may be used. It may prohibit, for example, the creation or transmission of offensive or obscene materials. It may clarify how users can use personal devices on company premises. It may provide information around the repercussions of violations.
In short, acceptable use guidelines should help users to understand how business technology is meant to be used.
Permissions and access levels.
Permission and access levels should also be determined in your manufacturing IT policy. The policy should address what level of users are able to access certain resources and preclude lower-level users from accessing resources without authorization.
Password protocols.
Your IT password policy should provide regulation around password protocols. What will be acceptable as a password? Is there a password management platform you encourage employees to use? How can passwords be recovered?
Incident response.
Finally, your IT policy should deal with your protocols for incident response. In the event of a cybersecurity incident, preparation can go a long way toward minimizing damage.
You should document in detail how response will work – who will coordinate efforts, how communication will work, and what measures you might take to minimize the effects of a breach or hack.
Get more detail on how to create a manufacturing IT policy here.
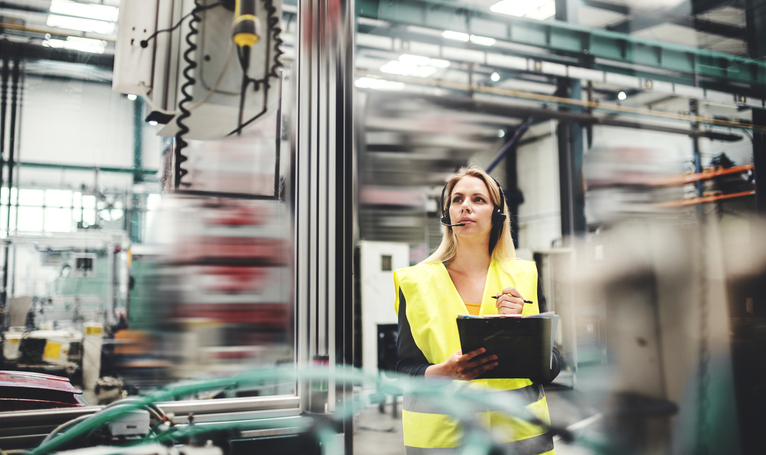
What are the top IT challenges for manufacturers?
Manufacturing companies face a unique set of IT challenges. While these issues aren’t difficult to diagnose, they can be complex to address. The manufacturing firms that are able to manage them well will have a considerable leg up on their competitors.
Maintaining uptime.
This is the age-old challenge of manufacturing. Downtime (especially of the unplanned variety) is a killer; studies estimate that automotive manufacturers, for example, lose $1.3 million per hour that their systems are down. Predictive maintenance, which we discussed earlier, is one innovation that is helping to address this. At a general level, the takeaway is that IT system dependability is crucial.
Managing data.
Data management is another challenge area for manufacturers. The problem, increasingly, isn’t a lack of data; it’s an inability to use data to generate insights. Technology platforms are constantly generating data about production lines, supply chains, employee performance – the list goes on and on. Manufacturers have massive amounts of data.
The problem is that that data still may not be integrated (so, for instance, the data on employee performance may not inform production line activity). And, secondly, data is often not organized well in ways that are conducive to visibility.
The good news is that solutions like Microsoft Power BI can help greatly with these issues so that data can be used to make intelligent decisions. IT solutions that make data management more effective pay huge dividends.
Finally, manufacturers face intimidating cybersecurity challenges. From data breaches to hacks, firms face the very real potential of significant losses from cyber events. IoT networks are notoriously vulnerable to attacks, too. IT solutions for manufacturing must offer cybersecurity services.
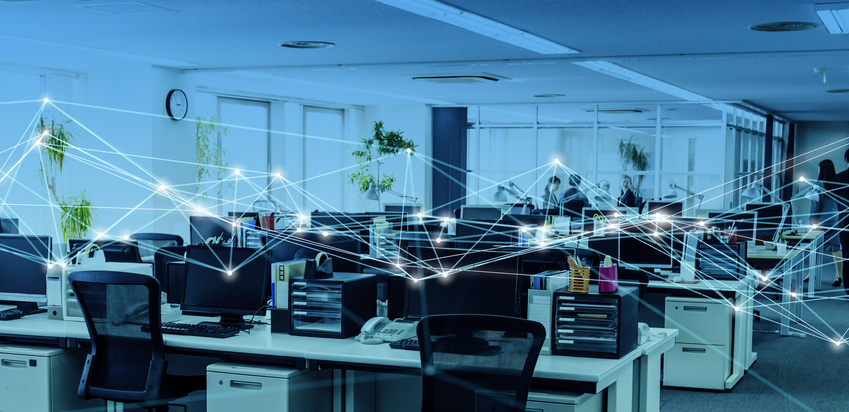
How should manufacturers approach cybersecurity?
The good news is that manufacturing facilities can reduce cybersecurity risk.
And, while the methods of reducing risk can become complex in application, in principle they’re fairly straightforward. To reduce cybersecurity risk, manufacturers should:
Document protocols.
As we’ve discussed previously, robust cybersecurity policies can lessen the likelihood of an incident in the first place, and response documentation can give teams quick paths forward to minimize damage in the event of an attack.
Train users.
Too many organizations don’t provide any sort of regular cybersecurity training to users; studies show that about 50% of companies offer little to no training on cybersecurity. Training users on best practices is an impactful way of reducing risk; ignorant user action leads to far too many successful attacks.
Make systems redundant.
Systems should be redundant, meaning that there should be multiple instances of mission-critical data and systems so that if one instance is compromised, recovery is possible. Production lines and networks should be prepared, and manufacturers should diligently back things up. This greatly reduces the damage that a cyberattack can cause.
Harden systems.
In addition to backing things up, manufacturing companies should also take steps to harden systems. Doing this effectively will likely involve a risk assessment (which may uncover disturbing vulnerabilities – Varonis estimates that 21% of manufacturing files are exposed). Generally, solutions involve implementing antivirus or other security software, and may include proactive monitoring as well.
And, last, but not least:
Get help.
The best way to counter cybersecurity risk for manufacturing is to work with an expert IT firm that can enact all of these principles in your environment.
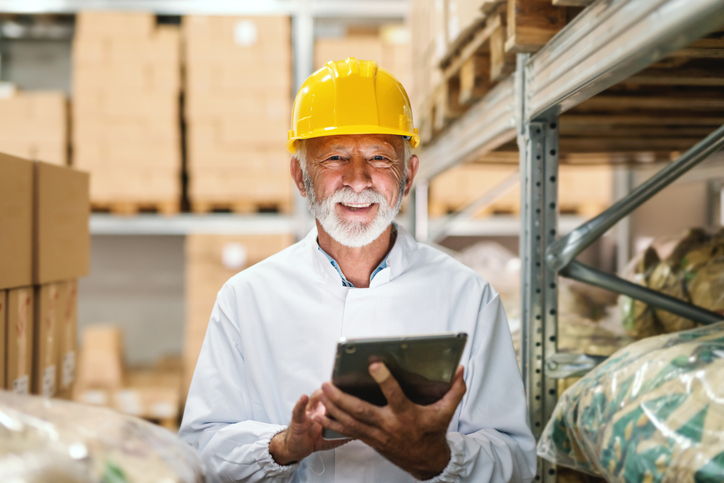
What ERP solution is best for manufacturers?
We’ve mentioned ERP solutions several times so far – for good reason. These platforms are the foundation of efficient manufacturing processes. Now, let’s take a look at a few of leading options.
Microsoft Dynamics
There are a variety of Microsoft Dynamics solutions, including GP and 365 (and within that, Business Central). For most mid-to-large manufacturing firms, Dynamics 365 is an outstanding option.
Here’s how Microsoft describes its effects on operations management: “[Dynamics 365 allows you to] move from reactive to predictive operations, automate and simplify your manufacturing and supply chain management, and maximize the life of your assets.”
At ATB Technologies, we can help you design and implement a Dynamics solution that’s perfectly tailored to your environment. We can also tailor existing solutions to your needs.
NetSuite Manufacturing
NetSuite Manufacturing (from Oracle) is another major player in the manufacturing ERP space. Their solution offers production, inventory management, demand management, a CRM, and financial data inside of a single, cloud-based system.
Here’s how they describe it: “No two businesses are the same and NetSuite’s industry-leading cloud manufacturing software offers the power and flexibility you need to support the evolution of your business – from the shop floor to the top floor.”
Acumatica Manufacturing Edition
Finally, Acumatica is another (smaller) player in the manufacturing ERP space. They’re cloud-based, as well, and their solution integrates manufacturing, inventory management, and accounting.
Here’s how they put it: “[Acumatica] delivers powerful and comprehensive functionality for make-to-stock, make-to-order, engineer-to-order, project-centric, job shop, batch, and repetitive manufacturing companies.”
Again, your ERP is one of the biggest factors in your success or failure. To ensure that you’re getting the most out of your solution, we recommend that you get a free consult. Our team of developers is all in-house and based right in St. Louis. We can help you make your technology an advantage.
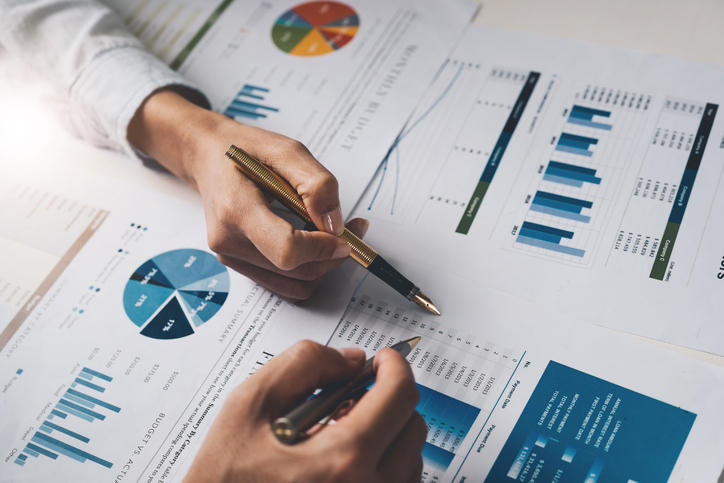
How can manufacturers use data analysis?
After our ERP software analysis, let’s look at one more topic of concern for manufacturers: data analysis. We’ve stressed again and again that data is important. But how can data analysis be done in a way that actually impacts business results?
Track and visualize data.
It starts, obviously, with tracking data. Importantly, this means tracking the right data. Again, an optimized ERP solution is a great start toward this. Business analytics tools (like Power BI) can help to visualize data in ways that allow for insight.
Integrate and optimize processes.
With data tracked and visualized, you’ll be able to bring efficiencies into your processes. You’ll be able to integrate across processes, giving you a fuller picture of your facility’s operations.
Make data-driven decisions.
Finally, a general point: data should inform decisions.
You need data to recognize that COGs are too high (so that you can potentially reevaluate your relationships with suppliers). You need data to determine how effective quality control efforts are (so that you can potentially change them). You need data to determine the level of output you can realistically expect (so that you can communicate accurately with vendors). In short, you need data to make decisions.
Data analysis should focus on giving you the data that will be most impactful in improving your decision-making.
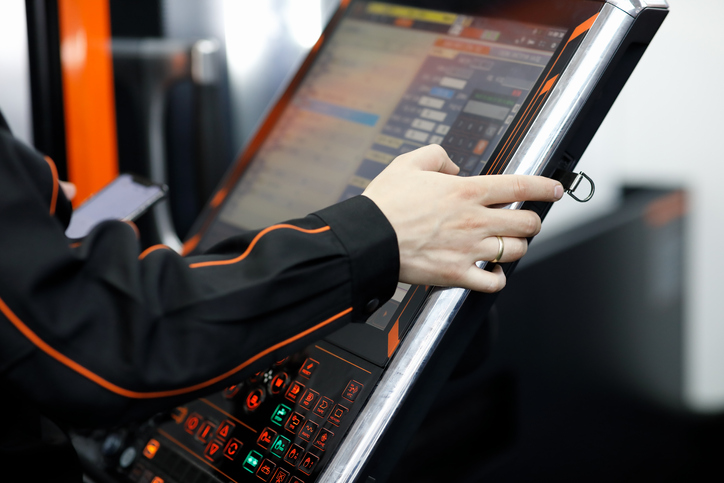
Ready to get started with IT support for your manufacturing?
As we’ve seen, technology is critical in manufacturing success. To succeed in the 2020s, your manufacturing company needs technology that provides an advantage.
At ATB Technologies, we can help.
We provide manufacturing IT support, including ERP consulting and managed IT services. We’re differentiated by our lightning-fast response, tailored end-to-end solutions, and proactive approach. And our engineers are experts you’ll enjoy talking to. If you’re ready for technology solutions that will give you an advantage, get in touch with us today for a free consultation
Ready to Turn IT into an Advantage?
Fill out the form below to request a quote, and one of our friendly consultants will be in touch shortly. We’ll discuss your needs and take the first step toward better IT.